Manufacturers always strive to better their operations that would lead to the growth of their organizations. Enterprise Resource Planning (ERP) software is an important tool that has changed the manner in which businesses handle their resources and processes. The Enterprise Resource Planning (ERP) systems involve aspects such as finance, inventory, production, and human resources that can be integrated into one platform to enhance efficiency in operations and decision-making.
This article discusses how ERP can change the game for manufacturers almost as it cuts costs and creates profits, improving competitiveness in the market for long-term success.
What is Enterprise Resource Planning?
Enterprise Resource Planning, popularly referred to as ERP (wiki), is an integrated software system created to converge and rationalize different business processes in an organization.
It serves as an atomic-kind platform by linking up departments such as finance, human resource management, supply chain, and manufacturing among others to ensure prompt communication and data shared across organization.
A company with ERP acquires more control, visibleness, and efficiency thus allowing it to make more rational decisions, optimize resources, and enhance the overall productivity.
Related: How Enterprise Data Warehouse Impacts Businesses: Concept and Benefits Explained.
Importance of Cost Reduction and Profitability in Manufacturing
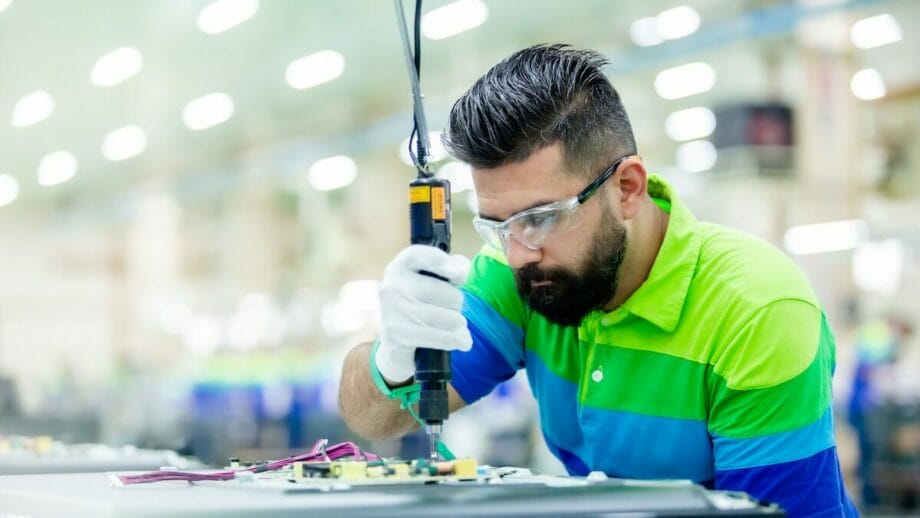
Cost reduction and profitability are not just a wish in the manufacturing industry but keep them alive in this business. Having to cope with increasing raw material and labor costs as well as intense competitive pressure continues to be a challenge for manufacturers. This would touch directly on the company bottom-line, pricing competitiveness, and provide investment resources for innovation and expansion.
Similarly, increased profitability provides a firm financial base for such businesses during market variations and to undertake future projects. Through improved processes, resource management, and decision-making, ERP systems are central to achieving such goals. Modern manufacturers use the ERP, which is a must-have to promote cost-effectiveness and profitability.
Understanding Manufacturing Costs
The manufacturing costs include all expenses relating to the production of goods. Considering that such costs are key to the activities of manufacturing and have high implications on a company’s profit margins. In order to costs down and be more profitable, a clear understanding of the elements or things that make up the price is essential. Here are some key elements of manufacturing costs:
Raw Materials
The most important components of the production process are raw materials. These may be direct materials that make up a part of the finished product or indirect materials not becoming an integral part. Cost of production is directly influenced by variations in raw material prices; thus, proper sourcing and inventory management are crucial.
Labor Costs
The labor costs consist of the wages and benefits paid to employees involved in production. This incorporates direct labor like assembly line workers and indirect labor such as supervisors and clerks. The management of labor costs depends on the optimization of efficient workforce productivity, the minimization on overtime, and in proper training.
Overhead Costs
Overhead costs are indirect and non-uniform expenses which receive no definite relationship to a specific product but can help organize general production. Such costs may comprise items like rent of factory, utilities, maintenance expenses and depreciation of equipment, administrative expenses as well as other indirect manufacturing costs. However, overhead costs are difficult to properly allocate to a particular product but greatly affect the structure of total costs.
Energy and Utilities
The manufacturing processes often involve high energy input including electricity, gas, or water. Energy costs may vary due to market and production variables. By adhering to eco-friendly practices and employing efficient technologies, one can realize huge savings in the long run.
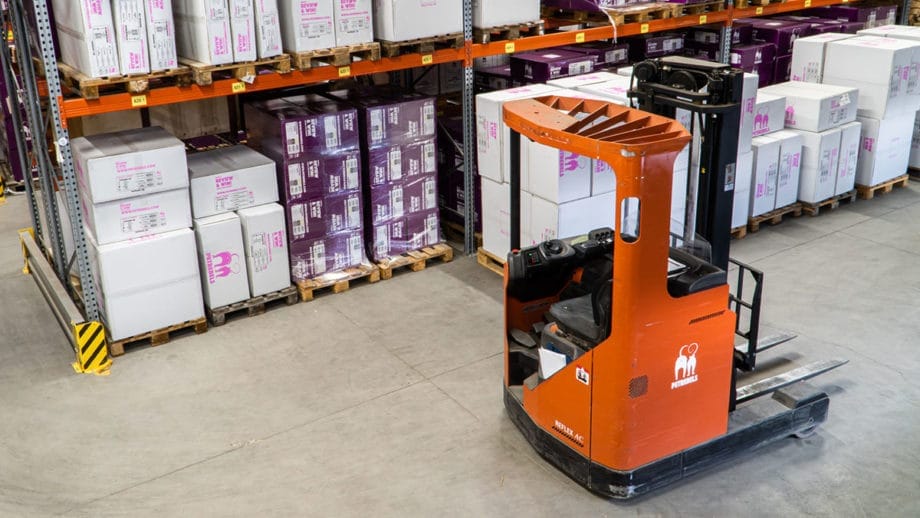
Inventory Costs
The carrying costs include storage, insurance, and potential obsolescence associated with holding excess inventory. Conversely, insufficient inventory causes late production and loss of sales. For minimizing costs and keeping every customer satisfied, achieving the right balance via effective inventory management is anybody’s aim.
Quality Control and Rework
In order to achieve customer satisfaction and minimize the returned or warranty claims, maintaining high quality products is essential. Efforts to control quality and any rework that may be needed can, nonetheless, increase the costs of manufacturing. Quality management systems can provide a way to detect and eliminate the problem in their early stages of production, therefore, curbing the overall high cost of poor quality.
Transportation and Distribution
The final cost associated with the case that comes up after the products have been manufactured is transportation and distribution costs. These include shipping, freight, and other logistics expenses of finished goods from the manufacturing facility to distribution centers or end customers.
Challenges in ERP Implementation
The next key challenge is overcoming challenges in ERP implementation, as they are critical to pushing through a transition to the new system. Some of these strategies are adequate planning turning to data migration, validation, and testing so that data inaccuracy is prevented. This involves affordable full staff training, and support thereafter to overcome resistance and encourage smooth adoption.
This is important so as to strike a balance between customization and standardization, while still considering scalability needed for the future business needs. Well-coordinated implementation also contributes to efficacious project management, stakeholder inclusion, and transparent communication. Selection of suitable vendors and evaluations after the implementation to make sure that they are helpful to determine a reliable ERP system.
Disruptions and errors are reduced by applying change management strategies and conducting robust tests. Through seeking out these challenges and addressing them proactively, manufacturing companies can successfully adopt ERP, get benefit from ERP investments, and prepare themselves for long term efficiency enhancements, cost savings, and improved profitability.
See also: Why You Should Implement Zero Trust for Your Enterprise?
Use of ERP in Manufacturing
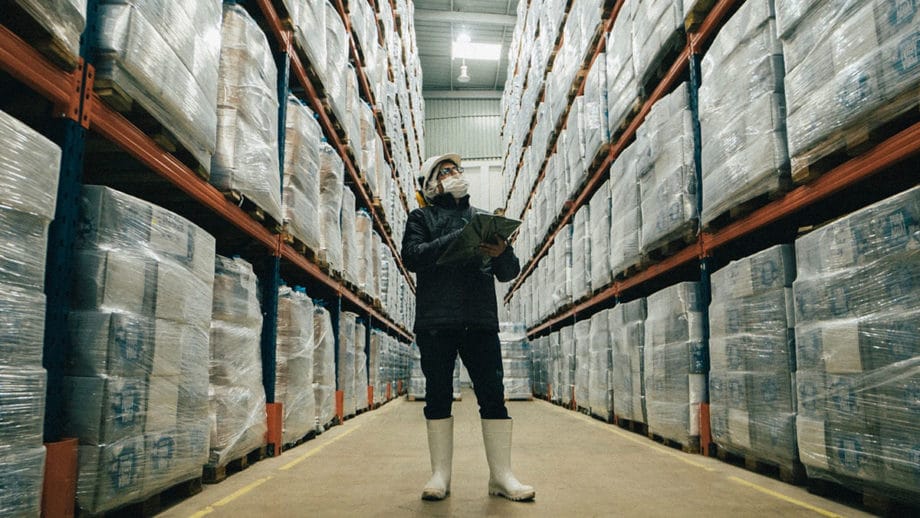
Enterprise Resource Planning (ERP) systems integrate and consolidate data from various departments in a company to provide an overview of the entire production process. ERP is the anchor for the new manufacturing as it changes how business is conducted, and resources managed.
Here are some key aspects of how ERP contributes to the manufacturing industry:
- Streamlined Processes: It includes automating and streamlining such complex business processes as invoicing, production planning, inventory management, and tracking of orders. This leads to improved operations efficiency and shortened lead times through the elimination of manual tasks and duplication of work.
- Enhanced Data Visibility: These systems provide instant availability of vital business information like sales, inventory levels, production schedules, and financial data. Such an arrangement guides management to take up informed decisions there and then spot opportunities for cost reduction and promptly respond to market or customer changes.
- Improved Resource Management: It assists in the efficient allocation of resources that includes raw materials, labor, and machinery. Manufacturers can monitor resource utilization and performance tracking, with a view to ensuring efficient resource utilization which leads to minimization of wastage in terms of resources and increased productivity.
- Effective Quality Control: Quality management can be facilitated by the ERP system which helps to incorporate quality control processes within the manufacturing workflow. Through such integration, quality checks are performed at critical stages minimizing the chances of defects and rework.
- Supply Chain Integration: With ERP, there is better supply chain integration with suppliers and customers. Such integration facilitates cooperation, reduces the complexity of inventory managing process, and allows better predicting of demand.
- Business Intelligence and Reporting: This leads to strong reporting and analytics, giving visibility into key performance indicators (KPIs) and trends. This data can be employed by the manufacturers to unveil cost reduction, process enhancement, and profit achievement.
ERP and Profitability Improvement
Manufacturing companies can achieve a higher level of profitability through an effective application of the ERP system. ERP enables companies to exercise greater control, visibility, and data-driven decision-making on their operations. Here’s how ERP contributes to profitability improvement:
Real-time Data for Informed Decision-making
The ERP systems provide time based critical business data access concerning sales, inventory levels, production schedules, and financials. This helps to facilitate timely management decision making, cost savings identification, as well as prompt response to market dynamics and customer calls.
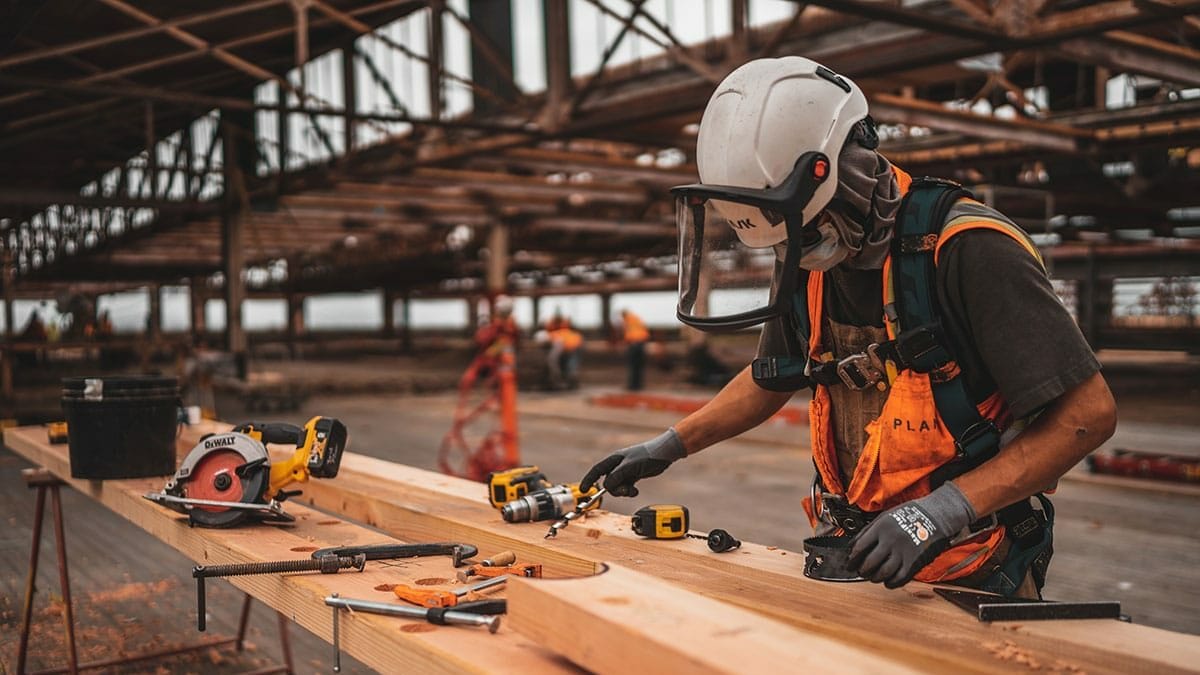
Cost Analysis and Reduction
Manufacturers can use ERP systems to do a detailed cost analysis. Companies can track raw materials, labor overheads, and such other costs of production to identify areas for cost cutback as well as improving the process. This increases the effective use of resources and hence declines operational costs, which go a long way in enhancing profitability.
Efficient Inventory Management
Manufacturers are able to manage their inventory effectively due to the ERP. Accurate data on stock levels, lead times, and demand patterns enable companies to avoid stockouts or overstock scenarios – thus lowering carrying costs, as well as ensuring a more efficient supply chain.
Production Planning and Scheduling
The use of ERP enables effective planning and scheduling for production by reducing downtime and optimizing the utilization of resources. Better planning helps manufacturers to get ahead of customer demand, avoid production stoppages, and improve overall productivity.
Customer Relationship Management (CRM)
Most of the ERP systems have CRM modules, which help manufacturers in handling customer interactions. Through keeping track of their customers’ preferences, feedback, and purchase history companies develop better customer services that satisfy the individualized needs of a specific one or group of customers. Therefore, it increases profitability due to higher customer satisfaction and additional business.
Identifying Profitable Products and Customers
Use ERP systems in product performance and profitability analysis for manufacturers. When companies understand which products yield the highest margins and which customers generate the most revenue, they can concentrate their efforts on highly rewarding opportunities enhancing profitability.
Financial Reporting and Analysis
Manufacturers can also use ERP systems to generate detailed financial reports, like revenue, expenses, and profitability in different business segments. Such insights enable companies to ascertain their financial strengths and weaknesses, make informed financial determinations, as well as allocate resources effectively for maximum profitability.
Related: Top 6 Best Enterprise SEO Tools You Can Use Now.
Final Thoughts

Adopting the ERP system may mark a turning point in cost retreatment and business profitability for manufacturing companies. ERP enables manufacturers to optimize their resources by improving its process simplicity, data visibility, and real-time insights. Successful ERP adoption depends on overcoming data migration, employee training, and customization challenges.
ERP integration enhances the efficiency of supply chain, inventory management, as well as customer relationships. Adopting ERP is a multi-paddled commitment to tech and a tactical cost in preparing for the foreseeable future manufacturing market.
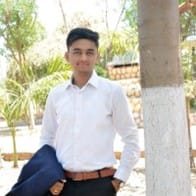